Producing and Exploring Ceramics with Kandura
Athina Ibrahim (A) meets with the team of Kandura Keramik (K)
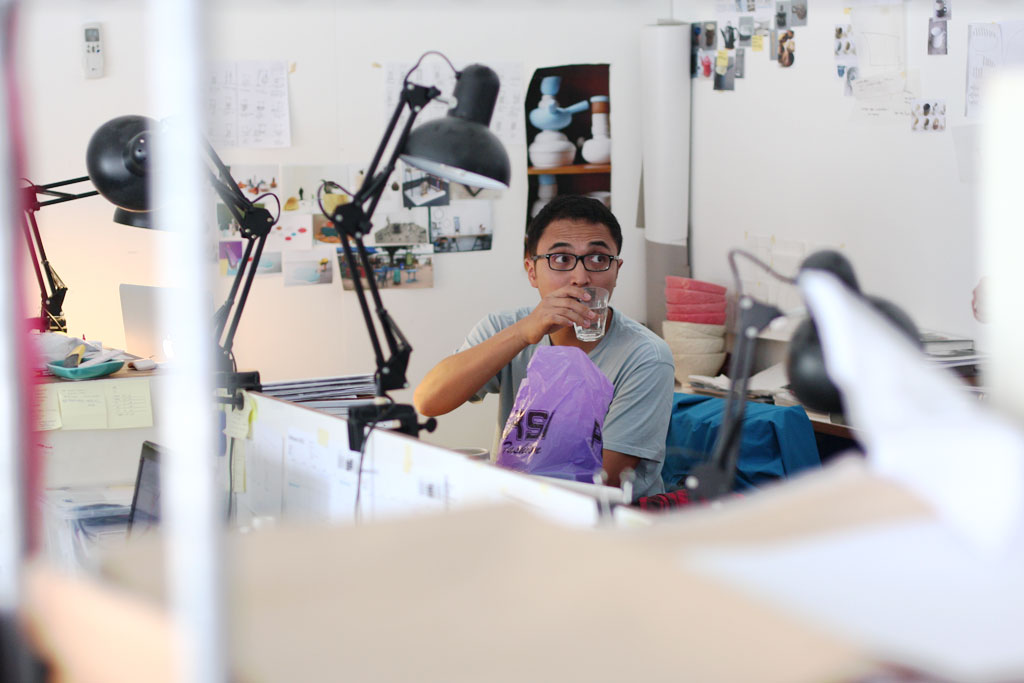
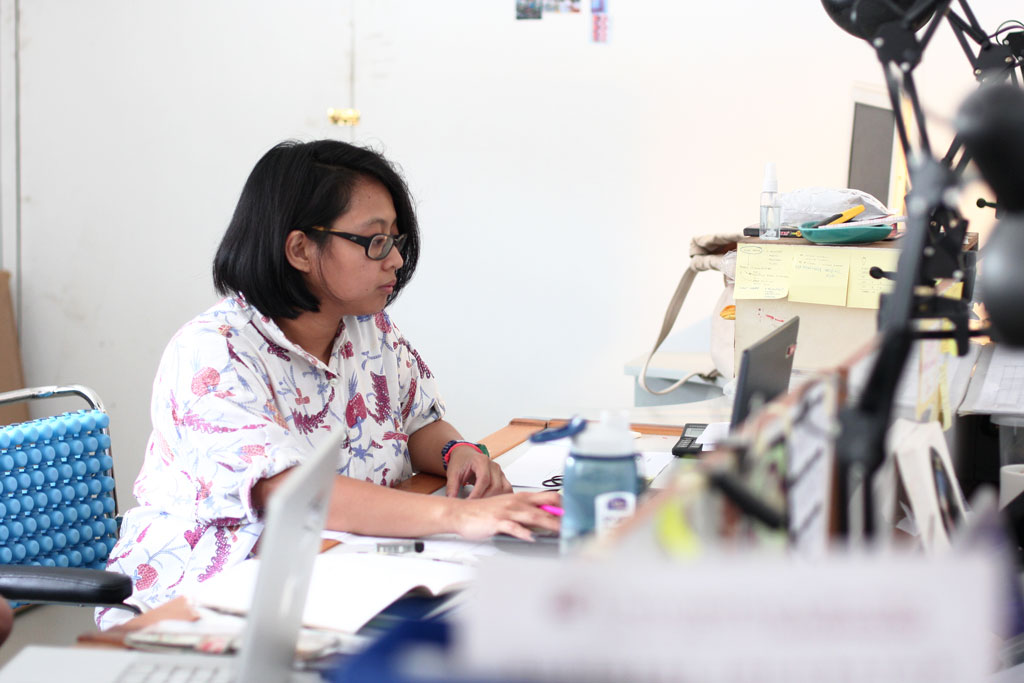
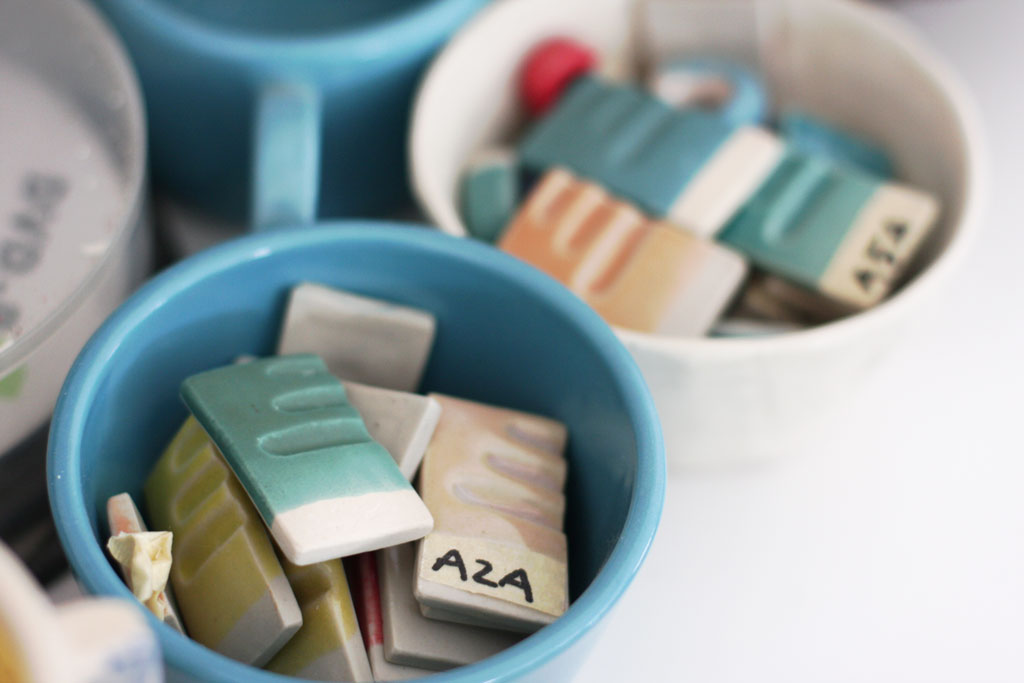
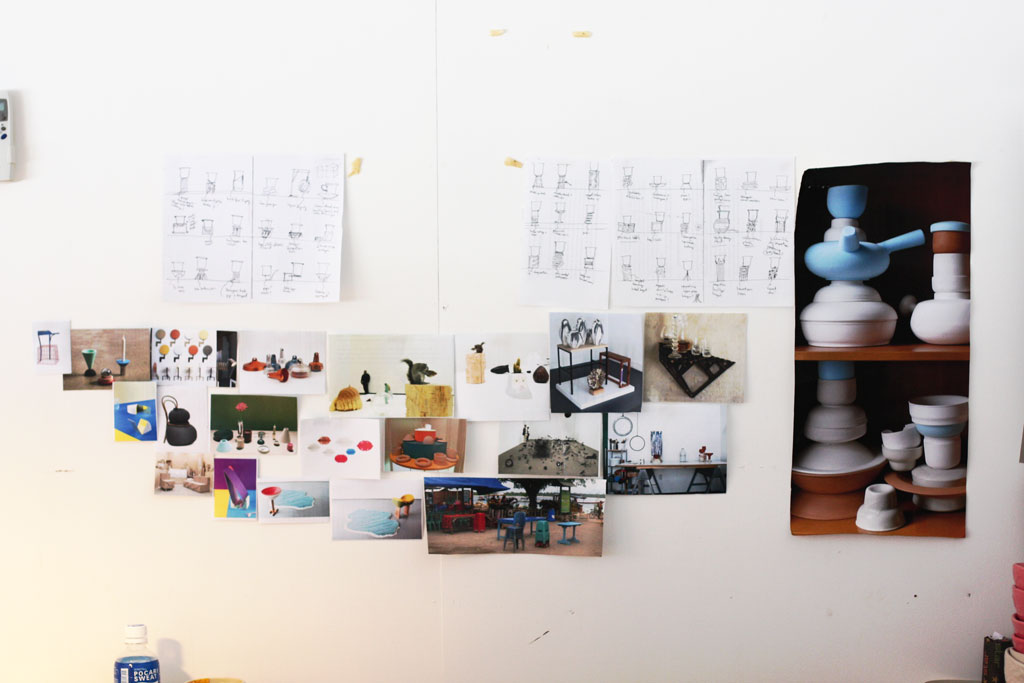
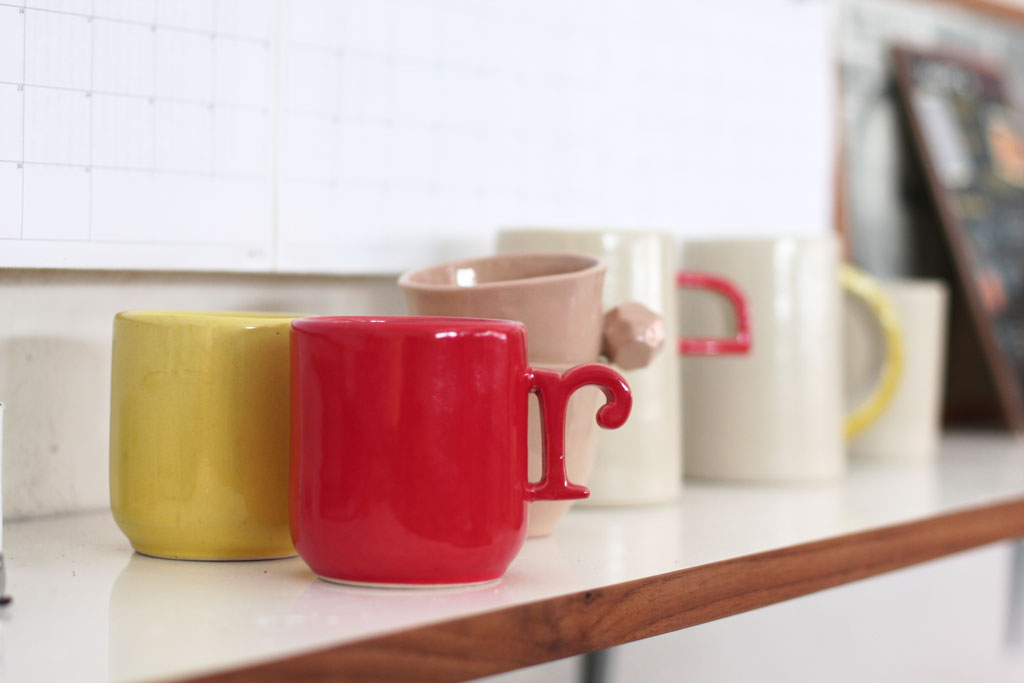
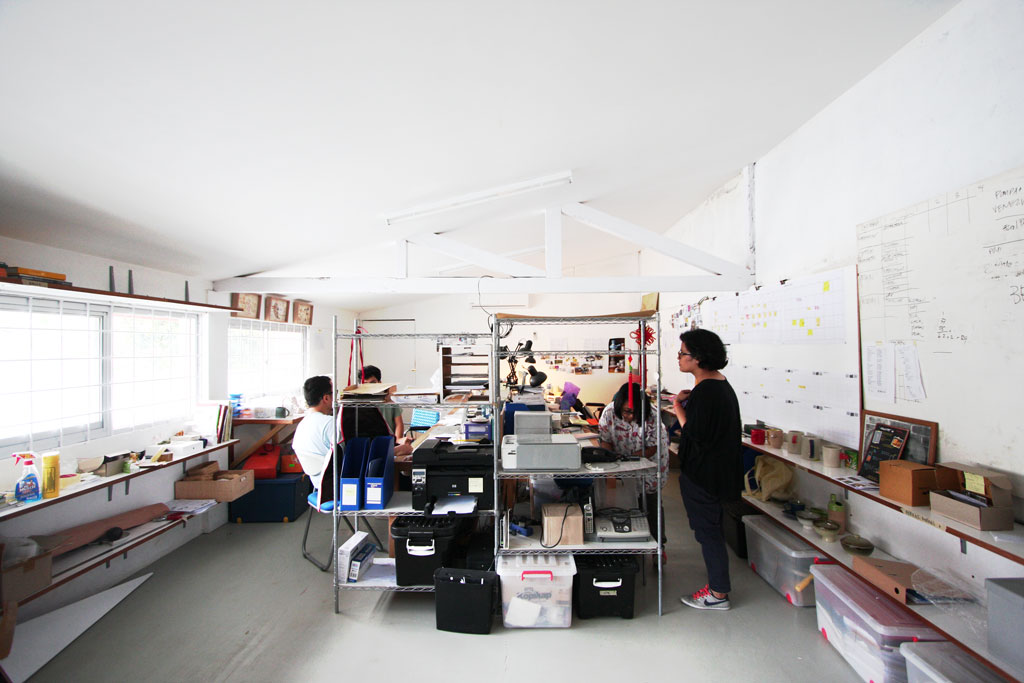
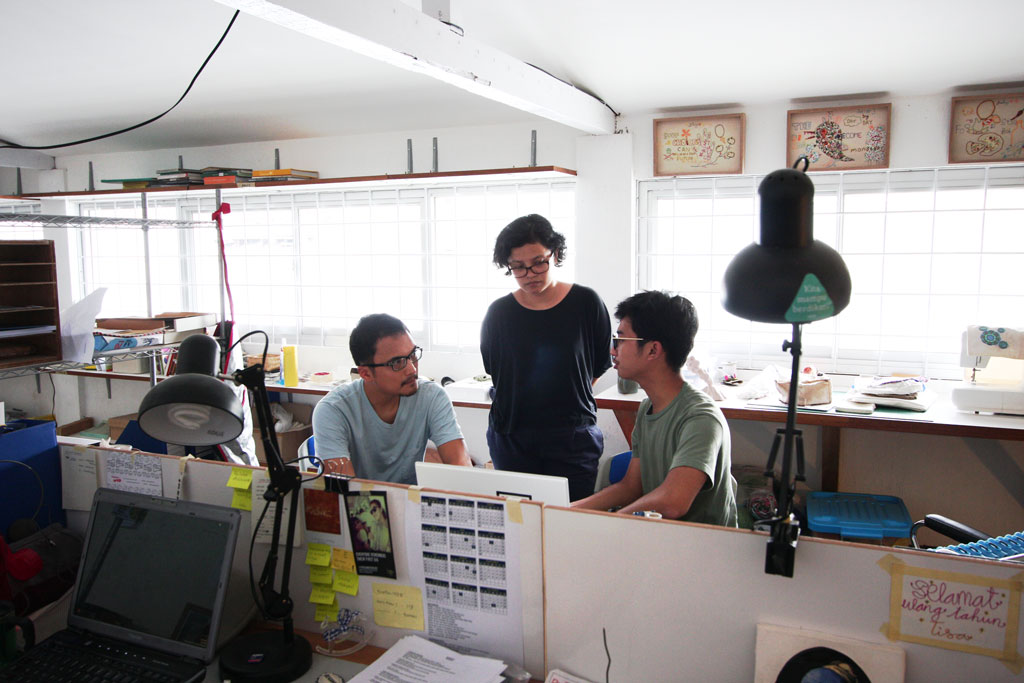
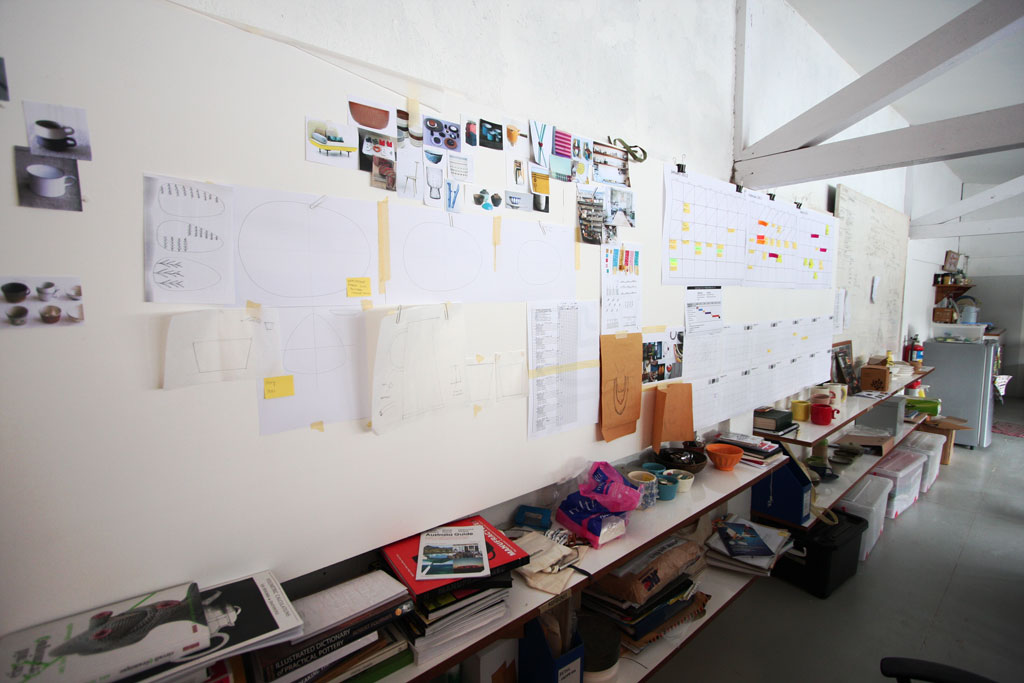
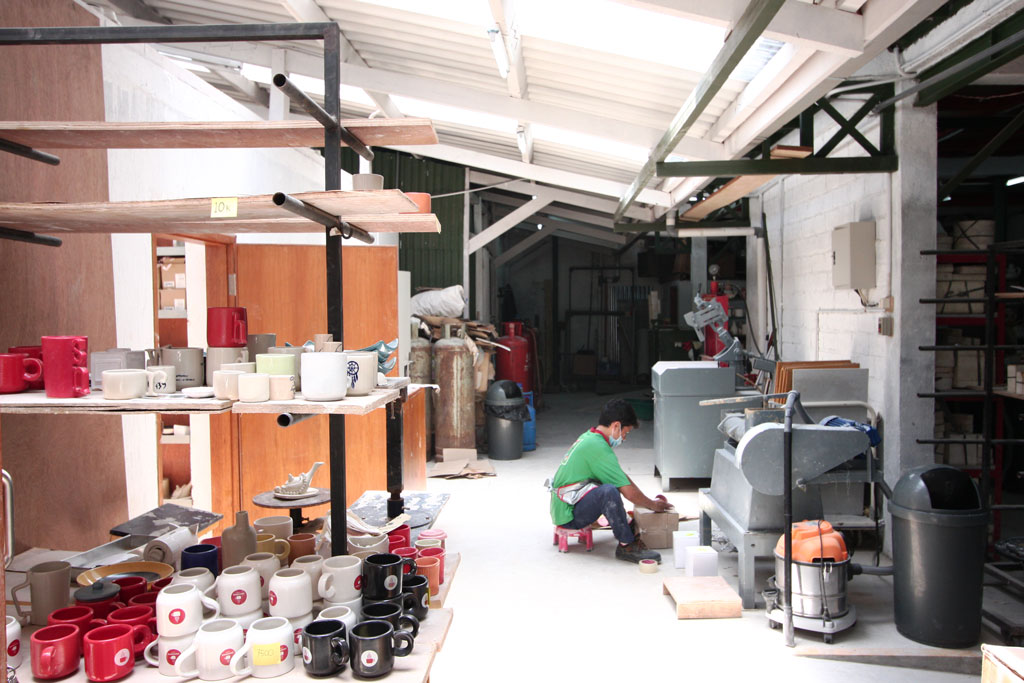
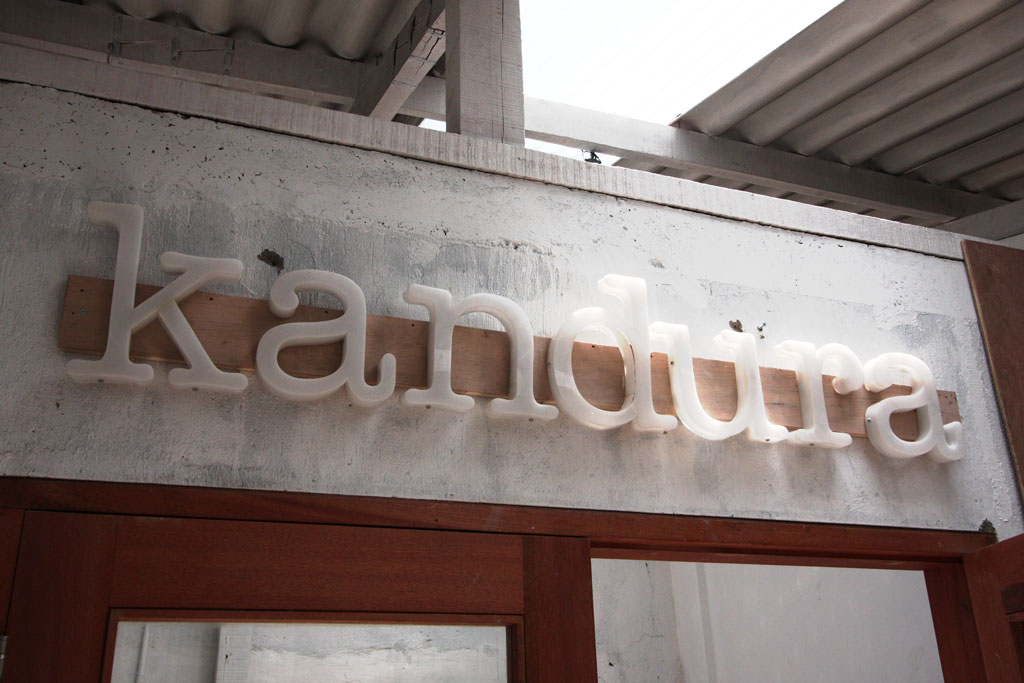
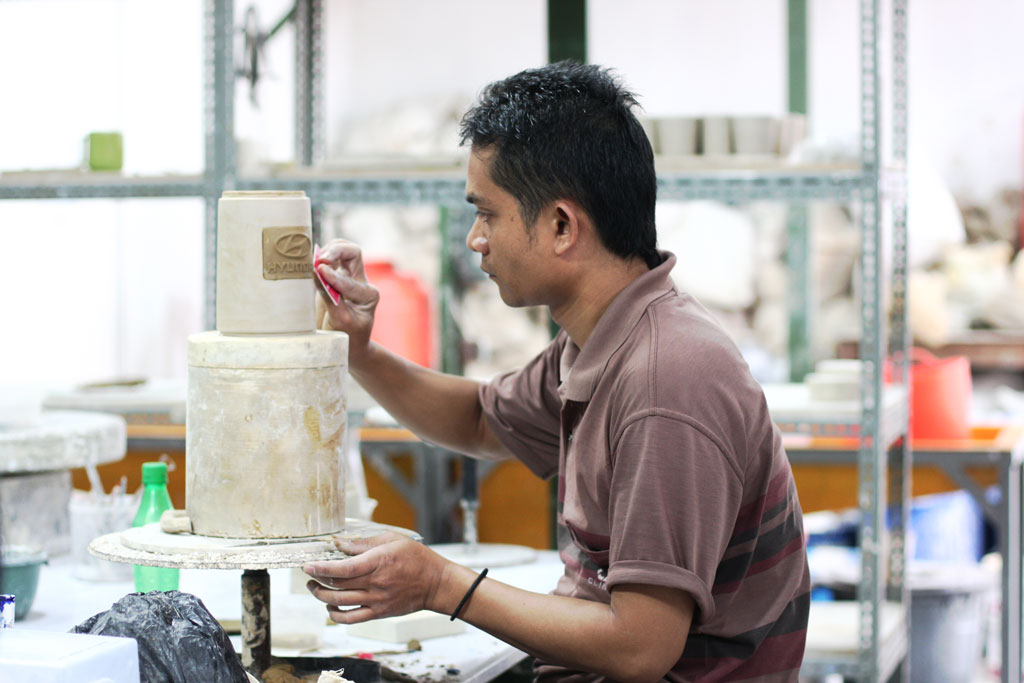
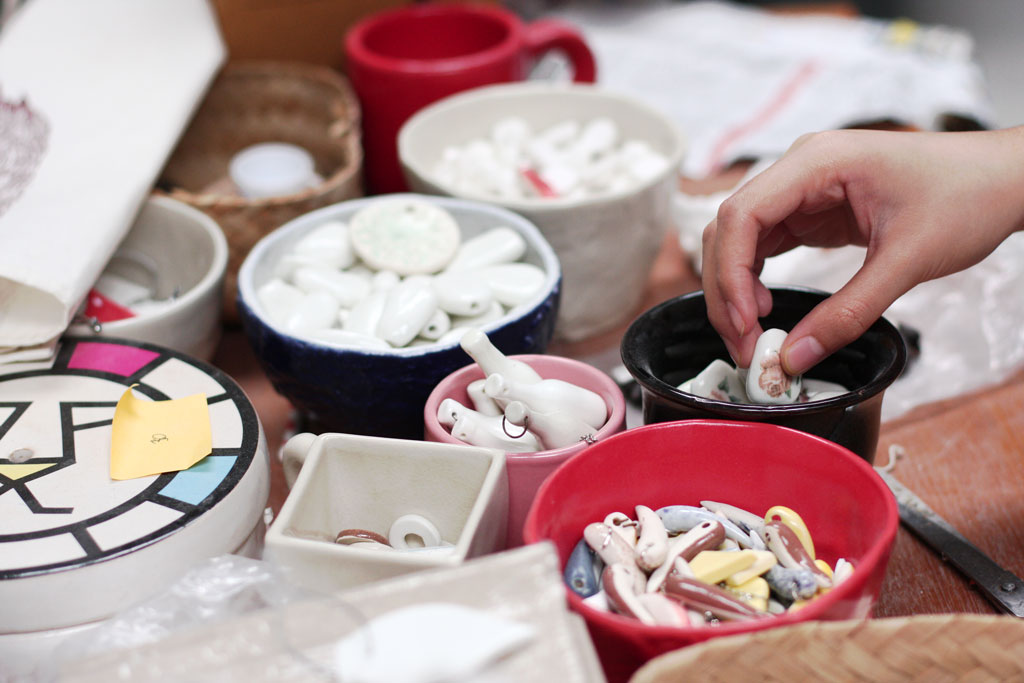
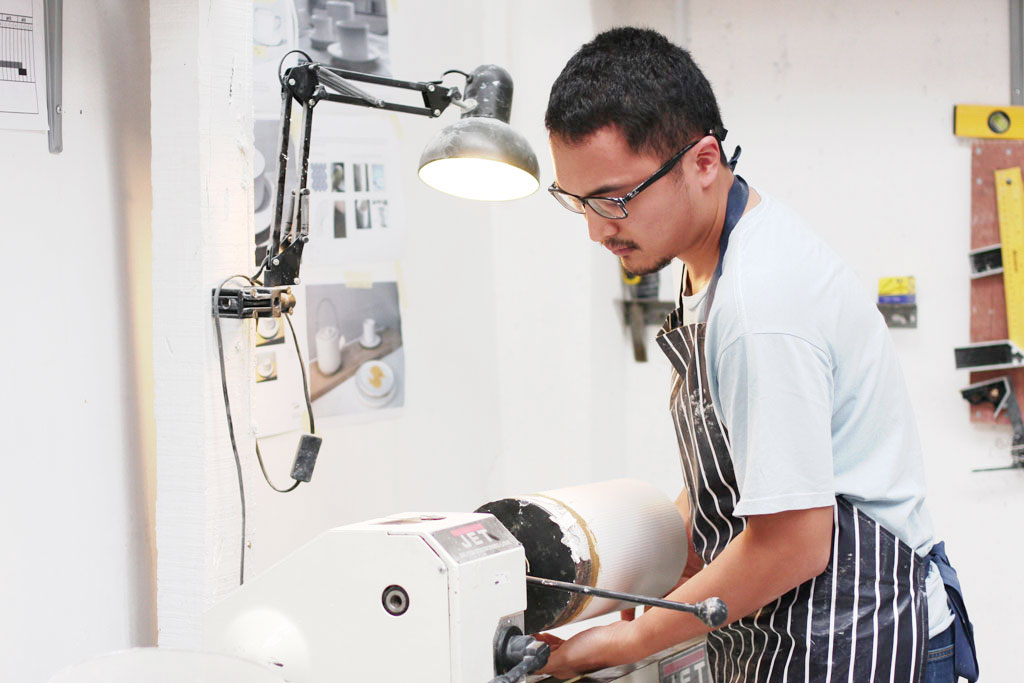
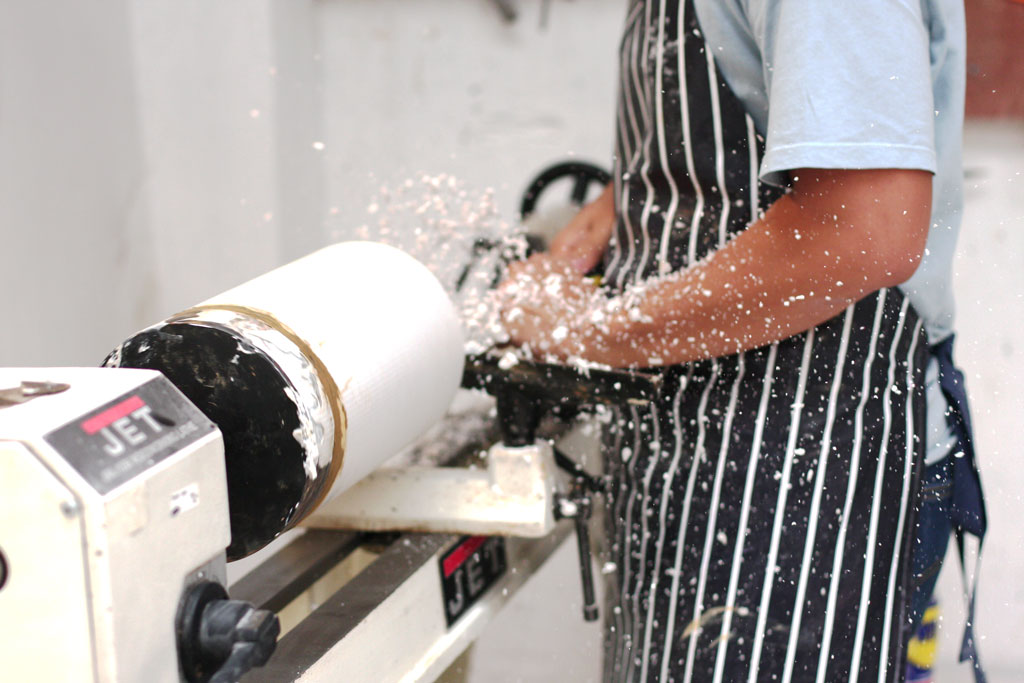

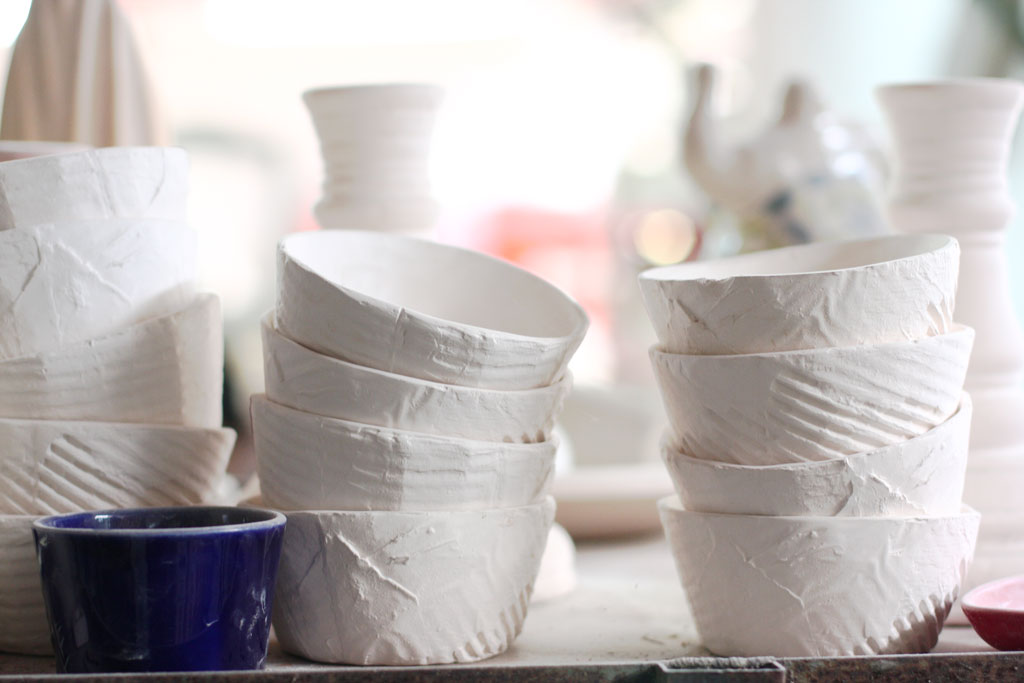
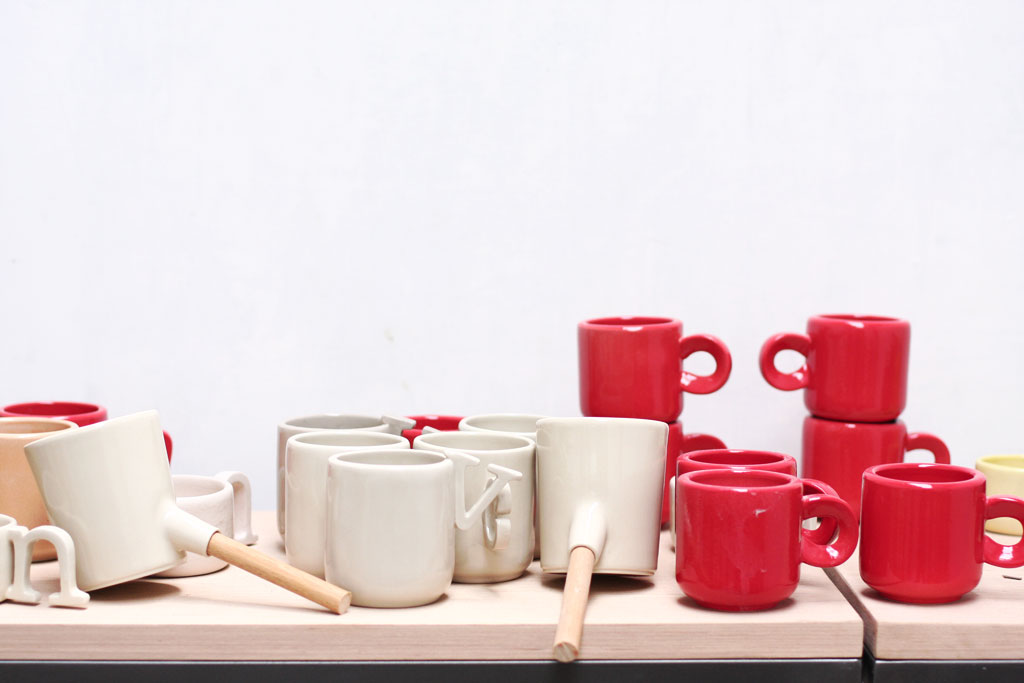
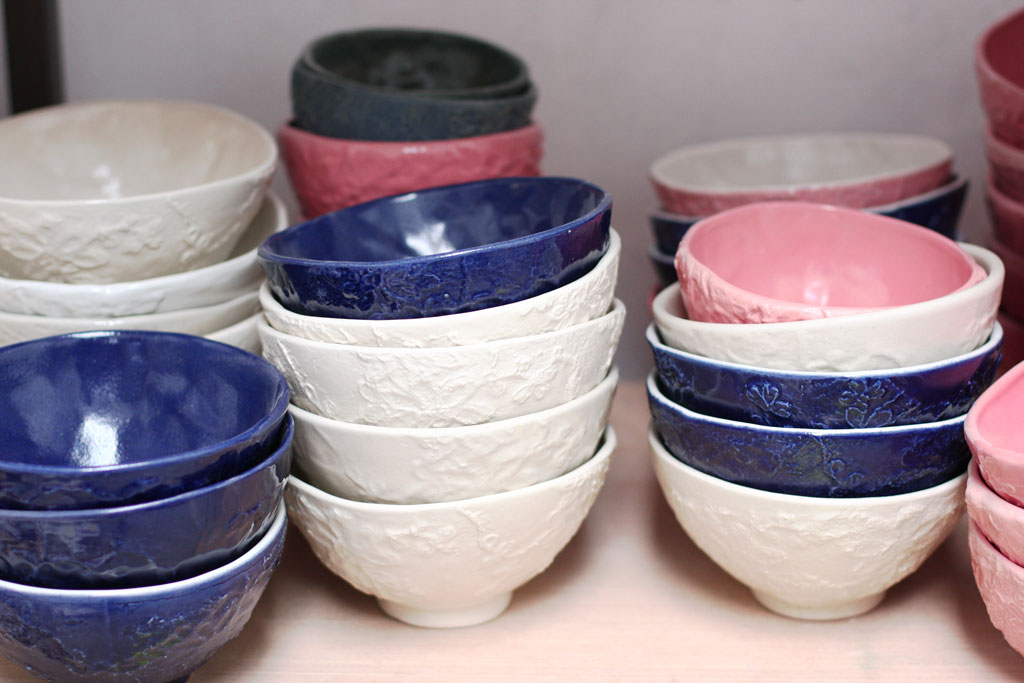
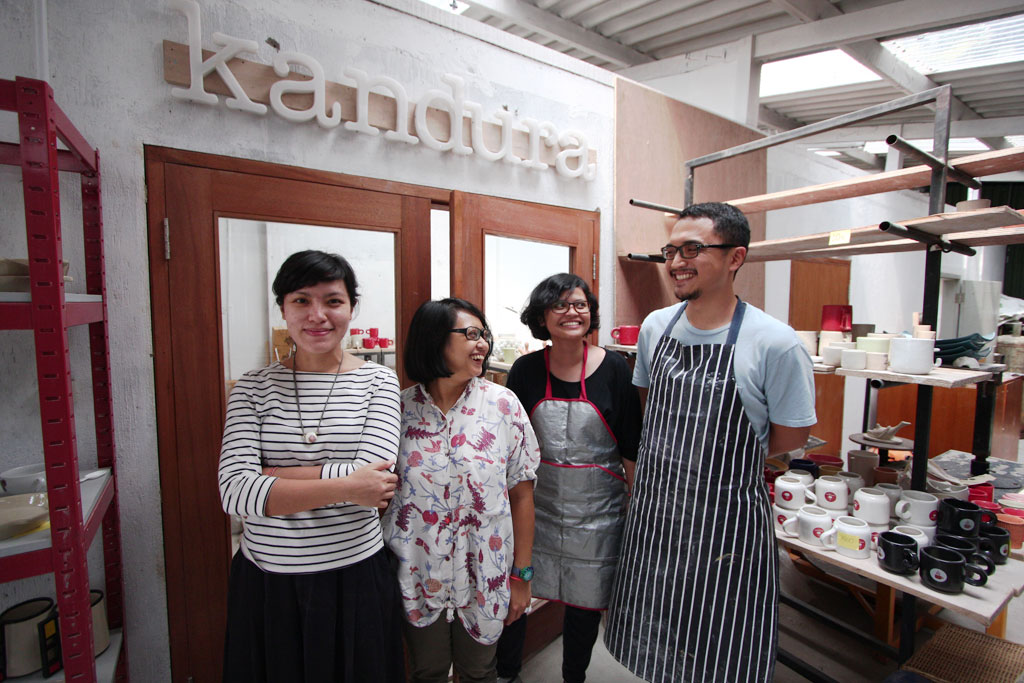
A
How did you guys gather together to form Kandura?
K
In 2005, most of us studied in the same university. Tisa and Uji were in the same batch at ITB and Ghia and Uji were neighbors. When we all graduated, Uji was the one who had the initiative to open a ceramic studio and asked all of us whether we wanted to join. Nuri joined a little later after the initial formation of the team.
A
What was all of your background?
K
Both Tisa and Ghia studied ceramic arts. Uji majored in product design but took a minor in ceramics and Nuri did something different from us, which was textile art.
A
What was the initial plans of making the ceramic studio?
K
From the start, we didn’t have any vision of making a start-up business. When we gathered the money for the studio, we only thought of refining our techniques in ceramic arts and to purchase the materials.
Our main goal, then, was experimenting with the varying materials and not making products to sell.
A
Can you tell us the story on how you ended up being a collective start-up?
K
It was still a long process until we got to the point of making it a business. We thought of it as a process of experimentation. As long as we were able to produce our own work, money was the last thing on our mind.
At the time, we all were doing our own thing – Uji decided to work in Bali, while Tisa spent time working at Soermardja Gallery – before we finally landed an artwork project that made us decide to have more focus on the studio.
A
What kind of projects did you focus on back then?
K
We weren’t doing ceramics products yet. If we did, we had to make sure of the kind of products we wanted to make and who our market would be.
One of our first few projects was an opportunity to work on a conservation project of Musuem BI. Our given task was to create a replica of their ceramic wall.
Initially, they approached a larger ceramic producer, but the specification requested to renovate the wall was on a smaller scale to what they’re used to producing, so they had to look for another option. We got this project by luck from someone who noticed we had ceramics dried at our studio porch. They offered the job and we took it. It took us 2 years to complete the project.
A
How would you make of the ceramic industry when you first started?
K
We haven’t entered retail by that point. We were still doing various ceramic projects. Ceramic isn’t something you easily find, there are so many variables involved, many components you need and countless of techniques to be accustomed with.
As an industry relating with design, the process isn’t standardized. With wood, the process is distinct and the treatment established. With ceramics, it can be very unpredictable and not measurable.
Until this day, our focus is still on finding the right materials, there are cases when we sample materials it would come out different than we expected, or when we find the right variable, suddenly the suppliers discontinues the product.
We also thought of using industrial waste in our designs, but for 3 – 4 years it gave a set of problems, the result wasn’t stable, so the manufacturing process had to go through a series of trial and error.
A
Have you found the right formula to make your ceramics?
K
Yes. We have almost found the solution…almost. It’s close to what we want but we, maybe, have to invest in more capital before we can get our ideal result.
We have made a series of adjustments but we don’t see this as a drawback, instead it becomes the character of the ceramics we make. You won’t find this character in other ceramic factories. That is what we try to offer.
A
When was the point when you realized Kandura had serious potential?
K
It was only at an ITB art market in 2006, we designed mugs and realized the appeal when it was quickly sold. By 2009, we took an opportunity to put our brand in together with 13 other brands at a store called Katallog. We then were invited to be part of an exhibition “We’re all Millionaire” by Chris Kerrigan and from then on we were invited to join Brightspot market.
A
What was the products that you offer?
K
One thing that brought us together from the start was tableware, back then we didn’t know the proper way of designing tableware. By 2010, Uji decided to continue his master degree in London and pursue ceramic arts in Central St. Martins. And that’s when we realized we were doing it all wrong (laughs).
A
You are based in Bandung and being in Brighspot Market had attracted big market in Jakarta, what can you understand from the market in both Jakarta and Bandung?
K
From what we observed, the buying power in Jakarta is really big. Price is not an issue. If they see something of quality that they like, they would immediately purchase it.
In Bandung, there are many who appreciate quality things, but most have the tendency to want to produce their own products – ceramic products may be difficult to make – but our friends who dwell in the fashion industry have the likelihood of having their products copied and made individually.
A
Why did you choose to be in Bandung?
K
Most of us are actually from Jakarta but studied in Bandung. When we graduated we weren’t in a rush to go back to Jakarta. We started the studio at Uji’s house and realized we had contacts to suppliers in Bandung. It was only natural to be in Bandung. Bandung, now, is way more enjoyable, you feel a sense of togetherness of the communities around. We would make friends with some of neighbors, who are also pursuing their own start-ups and it always gives us a great motivation to exchange ideas and experience.
In retrospect, if we started in Jakarta, maybe we would be in Jakarta. It doesn’t necessarily mean Bandung is our comfort zone, we just have more freedom in Bandung. We always try to challenge our comfort zone by being more discipline at work, we start as early as 8 am, and work according to schedule we make.
We also enjoyed the distance between our market in Jakarta and being in Bandung. Being in Bandung helped us have more autonomy in the things we designed without being influenced with what the market in Jakarta is hoping for.
A
Now that you have set up your own studio and workshop, how would describe each of your role?
K
All of us here are partners, but our responsibility are divided. Uji is focused on design, Tisa is involved in production and ceramic materials, Ghia handles the branding aspect, and Nuri handles various details of our work process including ensuring our clients are happy (laughs).
A
How would you describe working process? is the design handled by one person only?
K
Actually all of us are involved. Our recent project of making “Mugging Kandura” was handled by all four. We had the need to always work on experimental projects. By making a short project, we knew, we could see the immediate result. Uji first made the a generic mug prototype and everyone else was then given a design excercise to finalize its handle, our main job was to discover how this additional handle can be reintrepreted by its final user. We all were given the liberty to create our own interpretation of this brief.
A
How would you describe Kandura’s personal style?
K
We’ve played around with the materials we used and make sure what we design is something honest. We try not to imitate but keep the process natural until it evolves into something we enjoy and like.
We always try to combine things we like in our work, suppose Nuri has a background in textile, we try to incorporate it in the design.
A
What references do you use in your work?
K
We find many different references from the internet, magazines, and blogs. A lot of our visual references are taken from printed magazines as monocle to online publication as fffound or design boom. Normally, anything that we find are visually appealing we would pin it on the wall and see what we can do with it.
A
Do you have a personal project?
K
Each one of us has a personal project but Tisa, can be said, as the most active one in making her own personal projects, she’s been involved in various exhibitions.
A
If you look back, is Kandura how you imagined it to be?
K
I think so, its close to what envision Kandura to be. For seven years, there was a time where we were quite absent at Kandura, probably our most unproductive phase. Some of us were going back to school and focusing on other matters. From the start, we always wanted Kandura to be a place where we can explore in design and make something out of it. Intially, we had other needs to tend to, like paying the bills, so even though our work still revolved around ceramics, we took as many commercial projects we could handle.
Now we’re trying to place more emphasis on the design of tablewares and take it more seriously. We are still finding a way to find the most ideal solution for our manufacturing process. Working with restaurants and hotels, we understood that they were expecting to have standardized results. Where in fact, that’s not what we do. So our dream now is to find ways to work with a manufacturer to design standardized tablewares that fits people’s request but ensure we can give color to the design by giving it more life.
A
What kind of legacy do you want to leave?
K
When we first started, we had no idea that we are now going to be entrepreneurs. There are so many milestones that we have accomplished and we realized, just to get to one point takes an adequate amount of time. So our point, here, is we want people to value those steps and each struggling process. In the end its a matter of believing in what you put into.